Unveiling the World of OEM Lathe Machining Parts Manufacturing
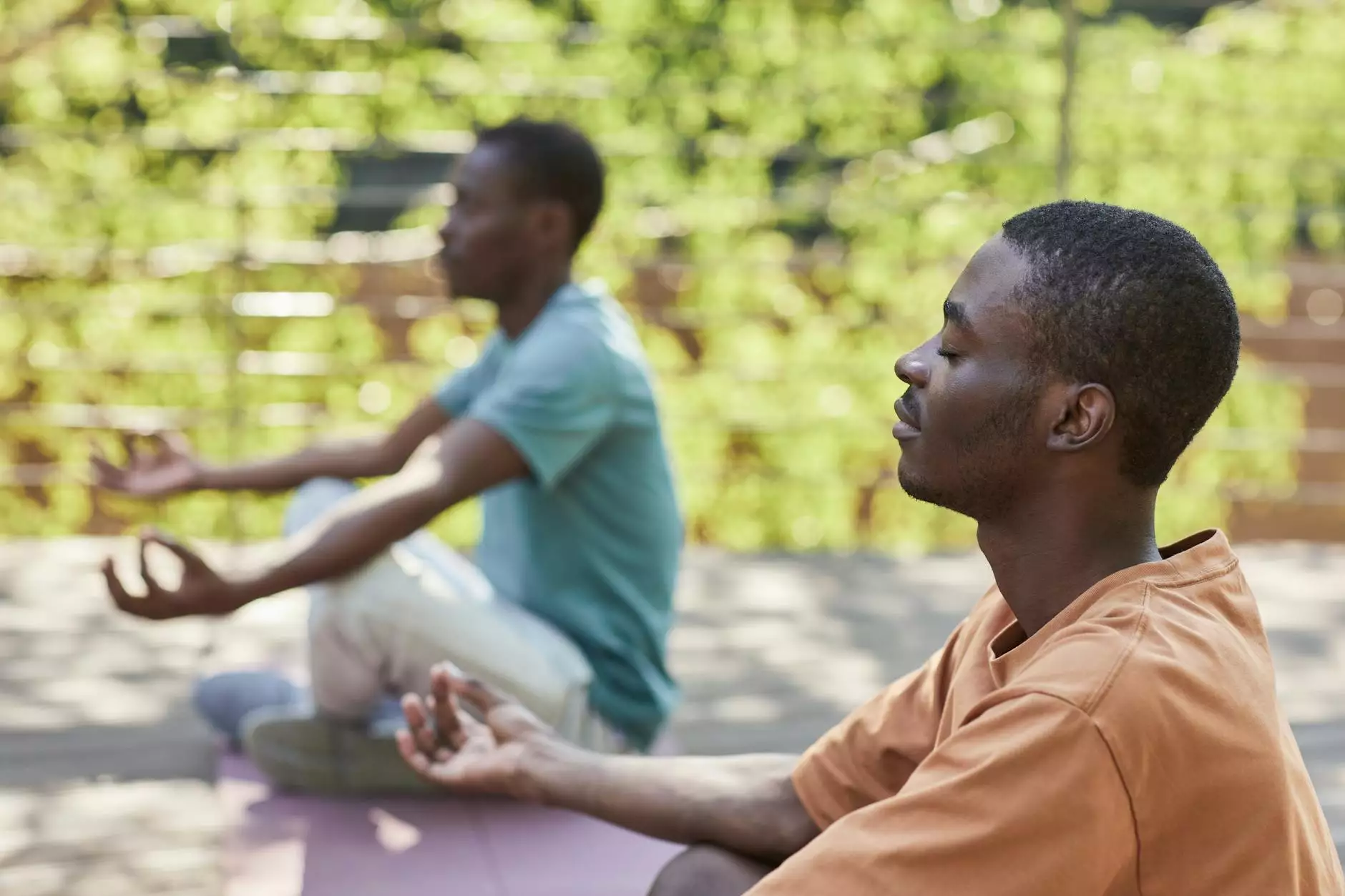
In today's fast-paced industrial landscape, OEM lathe machining parts manufacturers play a pivotal role in enhancing production efficiency and maintaining high-quality standards. As businesses strive for excellence, understanding the nuances of lathe machining and the benefits it brings is essential for success. This comprehensive guide aims to delve into the intricacies of OEM lathe machining, its advantages, and how partnering with a reputable manufacturer can elevate your business operations.
What is OEM Lathe Machining?
OEM (Original Equipment Manufacturer) lathe machining refers to the process of machining components that are specifically designed for end products of another company. This type of manufacturing is crucial in various industries, including automotive, aerospace, medical devices, and electronics. The precision and customization involved in creating machined parts ensure that they meet the unique specifications and demands of different applications.
The Importance of Precision in Lathe Machining
Precision is a critical component of lathe machining. The machinery used allows for extreme accuracy, which is essential in industries where even minor imperfections can lead to significant malfunctions. With advancements in CNC (Computer Numerical Control) technology, OEM manufacturers can create parts that are not only high-quality but also manufactured with incredible consistency.
Why Choose an OEM Lathe Machining Parts Manufacturer?
Partnering with an OEM lathe machining parts manufacturer has numerous benefits. Below are some of the key reasons why businesses should consider this route:
1. Customization and Design Flexibility
Every business has unique requirements, and OEM manufacturers are equipped to provide customized solutions. Whether you need parts crafted to specific dimensions, materials, or finishes, these manufacturers work closely with clients to design components that perfectly fit their needs.
2. Quality Assurance
Quality is a hallmark of reputable OEM lathe machining companies. They adhere to strict standards and often possess certifications that demonstrate their capability to deliver top-notch products. Rigorous testing and quality checks are integral to their processes, ensuring that every part produced meets industry-specific guidelines.
3. Cost Efficiency
While some businesses may hesitate to invest in OEM machining, the long-term savings can be significant. High-quality parts tend to have longer life cycles, reducing replacement costs and downtime. Moreover, the economies of scale enjoyed by established manufacturers often translate to competitive pricing for businesses.
4. Access to Advanced Technology
Experienced OEM lathe machining parts manufacturers continually invest in the latest technologies and equipment. This advancement allows them to leverage innovative manufacturing techniques, which can improve efficiency and reduce production time.
5. Expertise and Experience
With years of industry experience, OEM manufacturers possess valuable knowledge about materials, processes, and market trends. Their expertise allows them to provide insights and recommendations, helping businesses select the right materials and designs for their needs.
Applications of OEM Lathe Machined Parts
The versatility of lathe machined parts means they find applicability across various sectors:
- Automotive Industry: Custom parts for engines, transmissions, and other key components.
- Aerospace: Precision components subject to rigorous safety and performance standards.
- Medical Devices: Highly accurate parts essential for the functionality of medical equipment.
- Electronics: Components that need to fit tightly within smaller, intricate designs.
- Industrial Machinery: Parts designed for heavy machinery that require durability and reliability.
The Manufacturing Process in OEM Lathe Machining
Understanding the manufacturing process is essential to appreciate the capabilities of an OEM lathe machining parts manufacturer. Here’s a detailed look at the typical process:
1. Consultation and Design
The journey begins with a consultation, where engineers and designers collaborate with clients to determine specifications. This step often involves CAD (Computer-Aided Design) software to create detailed blueprints.
2. Material Selection
Material choice is crucial and can significantly impact the performance of the final product. Common materials used include aluminum, steel, bronze, and plastic composites, each chosen for its suitability for the intended application.
3. Precision Machining
Once the design is finalized, the manufacturing phase starts. CNC machines carry out precision machining, carefully shaping the material into the desired components. This process minimizes waste and enhances accuracy.
4. Inspection and Testing
After machining, each part undergoes strict quality control measures. This step may include dimensional inspections, surface finish assessments, and functional testing to ensure that parts meet the necessary standards.
5. Finishing
Finishing processes such as polishing, anodizing, or coating may be applied to improve the durability and aesthetics of the parts. This enhances not only function but also the product's appearance.
6. Delivery
Finally, once everything passes quality assurance tests, the parts are packaged and delivered according to the client’s requirements. Timely delivery is a key consideration for OEM manufacturers, ensuring minimal disruption to the client's production line.
Choosing the Right OEM Lathe Machining Parts Manufacturer
Selecting the right partner for OEM lathe machining can be daunting, but the following criteria can guide your decision-making process:
- Experience: Look for manufacturers with a proven track record in your industry.
- Certifications: Ensure they have relevant certifications such as ISO to guarantee quality standards.
- Technology: Evaluate their machinery and technology to ensure they employ modern manufacturing practices.
- Customer Reviews: Analyze feedback from previous clients to gauge satisfaction levels.
- Communication: Choose manufacturers who maintain clear and consistent communication throughout the process.
Conclusion: The Future of OEM Lathe Machining
As industries continue to evolve, the demand for high-quality, precision-engineered components is expected to grow. OEM lathe machining represents a vital avenue for businesses seeking efficiency, quality, and customization in their manufacturing processes. By choosing an experienced and reputable manufacturer, companies can position themselves for success, achieving greater productivity, lower costs, and superior products.
For those looking to enhance their manufacturing capabilities, partnering with an OEM lathe machining parts manufacturer like DeepMould.net could be the game-changer you need.
© 2023 DeepMould.net. All rights reserved.