Die Cast Mold Makers: The Backbone of Precision Manufacturing
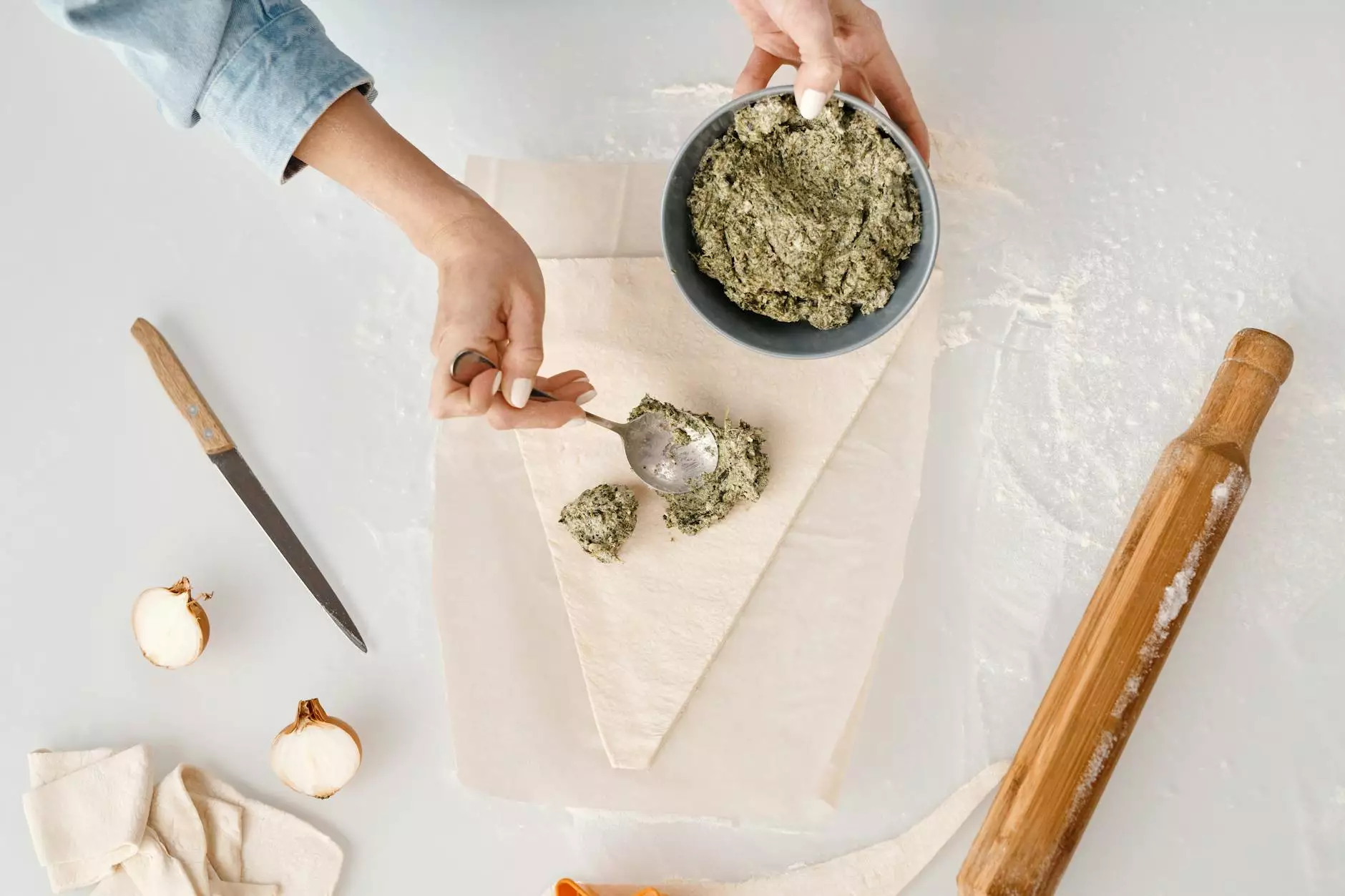
In the thriving world of manufacturing, die cast mold makers play an essential role that often goes unnoticed. This article dives deep into the intricate world of die casting and highlights the importance of high-quality mold makers like DeepMould.net in the metal fabrication industry. Through understanding the processes, benefits, and advancements in die casting, we can appreciate the craft and technical expertise that die cast mold makers bring to the table.
Understanding Die Casting: A Brief Overview
Die casting is a manufacturing process that involves forcing molten metal into a mold cavity under high pressure. This technique is primarily used to produce parts with complex shapes and high-dimensional accuracy. The end products are typically made of non-ferrous metals, such as aluminum, zinc, and magnesium, known for their lightweight and strong properties.
Key attributes of die casting include:
- High Precision: Die casting allows for intricate designs and detailed features to be achieved with minimal finishing work.
- Repeatability: Once the mold is created, thousands of identical parts can be produced in a consistent manner.
- Material Efficiency: The process minimizes waste material by utilizing exact amounts required for each component.
The Role of Die Cast Mold Makers
Die cast mold makers are craftsmen who specialize in creating the molds necessary for the die casting process. Their work involves significant planning, design, and execution to ensure that the mold meets stringent specifications and is capable of producing high-quality products.
Key Responsibilities of Die Cast Mold Makers
The responsibilities of die cast mold makers can be categorized into several key areas:
- Mold Design: Utilizing advanced software and engineering principles, mold makers design molds tailored to specific product requirements.
- Material Selection: Choosing the right materials for mold construction is crucial to withstand the temperatures and pressures of the casting process.
- Machining: Precision machining techniques are employed to manufacture mold components that fit together perfectly.
- Assembly and Testing: Once the components are fabricated, they are assembled, and the mold is tested to ensure it functions correctly under production conditions.
- Maintenance and Repair: Over time, molds wear out. Mold makers are responsible for the upkeep and repair to extend the life of the molds.
The Importance of Quality in Die Casting
Quality is paramount in die casting, and it directly impacts the performance and durability of the final product. High-quality molds lead to less waste, fewer defects, and an overall more efficient production process. Here’s why investing in quality die cast molds matters:
Reduced Defects and Scrap Rates
Using well-designed and expertly crafted molds minimizes issues like porosity, surface imperfections, and dimensional inaccuracies. This leads to lower scrap rates, which can save a business significant costs over time.
Enhanced Product Performance
Components produced using quality molds exhibit superior performance characteristics and longevity, critical factors in industries such as automotive and aerospace where safety and reliability are crucial.
Cost Efficiency
Although the initial investment in quality molds may be higher, the long-term savings from reduced waste, fewer production interruptions, and enhanced product quality outweigh those costs. Businesses that prioritize high-quality molds find themselves being more competitive in the marketplace.
Innovations in Die Casting Technology
The die casting industry is continually evolving, with technological advancements improving efficiency and quality. Some noteworthy innovations include:
Advancements in Material Science
New materials for die casting molds are being developed that offer greater thermal conductivity, wear resistance, and longevity. For example, the use of alloy steels and heat-treated aluminum is becoming prevalent.
Computer-Aided Design (CAD)
Modern CAD software allows mold makers to create highly detailed and complex mold designs quickly. This rapid prototyping capability ensures that adjustments can be made during the design phase efficiently.
3D Printing in Mold Making
3D printing technology is making waves in the mold-making sector, allowing for faster prototyping and the creation of intricate mold geometries that were previously unattainable. This technology reduces lead times and costs significantly.
Choosing the Right Die Cast Mold Maker
For businesses looking to optimize their die casting capabilities, selecting the right mold maker is a crucial decision. Here are some factors to consider:
- Experience: Look for mold makers with a proven track record in die casting across various industries.
- Technical Expertise: A knowledgeable team adept at utilizing the latest tools and technologies can significantly enhance mold quality.
- Quality Assurance: Ensure the mold maker has robust quality control processes in place to guarantee that every mold meets specifications.
- Customer Reviews: Check testimonials and case studies to understand the mold maker’s reliability and customer service track record.
The Future of Die Casting and Mold Making
As the manufacturing landscape continues to shift towards sustainability and efficiency, die cast mold makers must adapt to new demands. Factors influencing the future of die casting include:
- Sustainability: There is a growing emphasis on environmentally friendly manufacturing processes. Mold makers are being encouraged to adopt sustainable practices, including using recyclable materials and reducing energy consumption.
- Industry 4.0: Automation and the Internet of Things (IoT) are transforming the manufacturing sector, enabling real-time monitoring and predictive maintenance, which will impact mold-making practices and efficiency.
- Customization and Flexibility: As markets demand more tailored products, mold makers must develop molds that can accommodate varied designs without extensive reconfiguration.
Conclusion: The Vital Contribution of Die Cast Mold Makers
The expertise of die cast mold makers is fundamental to the success of the die casting process. Their skilled craftsmanship and attention to detail not only enhance product quality but also contribute to the overall efficiency and sustainability of manufacturing operations. Investing in high-quality molds and partnerships with proficient mold makers, like those found at DeepMould.net, is essential for companies looking to thrive in a competitive market.
Understanding the importance and advancements in die casting can empower businesses to make informed decisions that propel their manufacturing capabilities into the future. The foundation of quality die casting starts with exceptional mold makers who transform molten metal into robust, precision-engineered components that serve as the backbone of countless industries.